LVP offers you superior durability with wear layers up to 30 mils thick and waterproof protection that traditional flooring can’t match. You’ll find LVP costs $2-7/sq ft versus hardwood’s $3-12/sq ft, while requiring minimal maintenance compared to hardwood’s periodic refinishing. The click-lock installation system enables efficient DIY projects, completing within a day. Your choice between LVP or traditional flooring options depends on moisture exposure, traffic intensity, and budget considerations.
Key Takeaways
- LVP offers superior water resistance and durability at $2-7/sq ft, significantly lower than traditional hardwood flooring at $8-15/sq ft.
- Click-lock installation system makes LVP more DIY-friendly and faster to install compared to traditional flooring options requiring adhesives.
- LVP requires minimal maintenance with basic sweeping and mopping, while hardwood needs periodic refinishing and carpet demands regular cleaning.
- Wear layer protection of 12-30 mils makes LVP highly resistant to scratches and dents in high-traffic areas.
- Traditional flooring offers authentic materials but comes with higher costs and maintenance, while LVP provides durability with realistic wood-grain aesthetics.
Understanding LVP: Core Components and Materials
Modern construction has revolutionized flooring with Luxury Vinyl Plank (LVP), a sophisticated multi-layered system engineered for maximum durability and aesthetic appeal. At its foundation, you’ll find a robust backing layer that guarantees dimensional stability throughout the installation process. The core layer, constructed from high-density fiberboard or rigid vinyl, provides essential structural support and contributes to the overall thickness of this durable flooring solution.
LVP’s advanced printing technology creates wood-grain patterns that perfectly replicate natural hardwood, while the protective wear layer, measuring between 12 to 30 mils, shields against scratches and stains in high-traffic areas. You’ll appreciate the integrated underlayment that delivers superior acoustic performance and cushioning. This all-encompassing layering system transforms LVP into a high-performance flooring solution that combines the visual appeal of hardwood with enhanced durability and maintenance benefits that modern homeowners demand.
Traditional Flooring Options: A Comprehensive Overview
When you’re evaluating traditional flooring materials, you’ll encounter four primary categories: hardwood with its solid construction and natural wood grain, laminate with its multi-layer synthetic composition, tile featuring ceramic or porcelain construction, and carpet with its woven or tufted fiber structure. Each material type presents distinct installation requirements and performance characteristics, with hardwood averaging $8-15 per square foot installed, laminate at $3-8, tile at $7-20, and carpet at $3-10. Your selection criteria should factor in the material’s durability metrics, including Janka hardness ratings for wood (ranging from 1,290 to 3,680), wear layer thickness for laminate (measured in millimeters), PEI ratings for tile (scale of 0-5), and fiber density for carpet (measured in face weight ounces).
Common Flooring Material Types
Traditional flooring materials represent the foundation of residential and commercial construction, offering time-tested solutions for diverse applications. When selecting your flooring, you’ll encounter several primary categories: hardwood, laminate, ceramic tile, carpet, and natural stone. Each material presents distinct installation methods and maintenance requirements. Hardwood delivers lasting durability but demands regular upkeep, while laminate flooring offers a cost-effective alternative with click-lock installation. Ceramic tile excels in moisture resistance, making it ideal for wet environments, though it lacks the warmth of other options. Natural stone, including granite and marble, provides premium aesthetics but requires periodic sealing for protection. Carpet delivers comfort and sound absorption but needs consistent cleaning to maintain its appearance and hygiene.
Durability and Cost Analysis
Understanding the cost-benefit relationship between flooring materials helps determine their long-term value proposition. When you’re comparing LVP with traditional hardwood flooring, you’ll find distinct differences in durability and cost metrics.
Feature | LVP | Hardwood |
---|---|---|
Cost/sq ft | $2-$7 | $3-$12 |
Installation | DIY-friendly | Labor-intensive |
Durability | Waterproof wear layer | Requires refinishing |
LVP’s cost-effective nature is evident in both material and installation expenses, typically saving you $1-$5 per square foot compared to traditional options. While hardwood flooring represents a long-term investment lasting 30+ years, it’s susceptible to moisture damage and requires periodic maintenance. LVP’s waterproof properties and enhanced wear layer provide superior resistance to daily wear, making it particularly suitable for high-traffic areas where moisture exposure is common.
Durability and Longevity Comparison Between LVP or Traditional Flooring
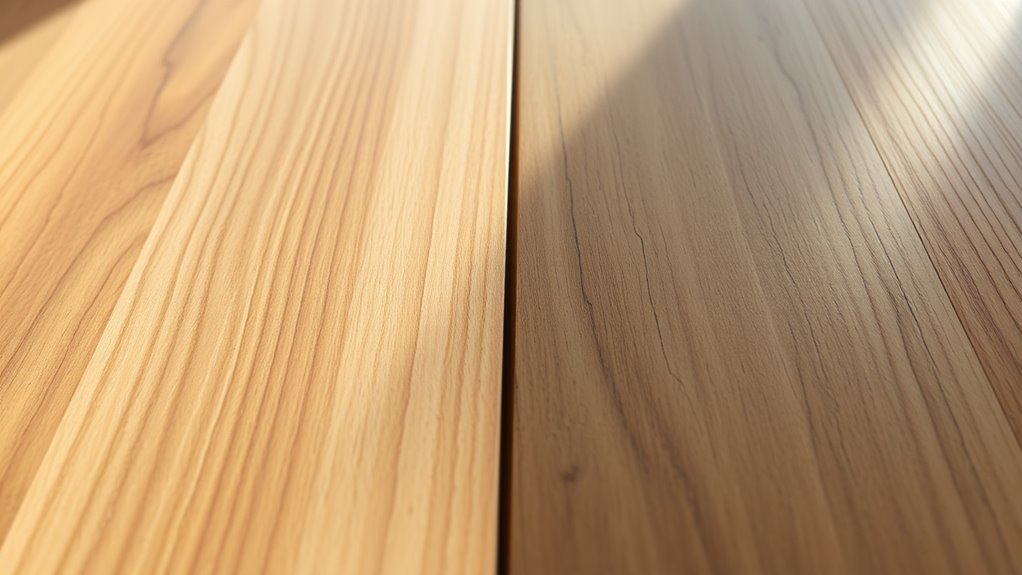
When you’re evaluating flooring options, LVP’s superior wear layer thickness provides enhanced protection against daily abrasion and impact damage compared to traditional hardwood’s vulnerability to scratches and dents. You’ll find LVP’s rigid core construction offers exceptional impact resistance, maintaining its structural integrity in high-traffic zones where traditional flooring often shows accelerated wear patterns. Your long-term cost analysis should factor in LVP’s minimal maintenance requirements and 20+ year lifespan against traditional flooring’s periodic refinishing needs, making LVP the more economical choice over time.
Wear Layer Protection Analysis
A crucial differentiator between LVP and traditional flooring lies in their protective surface layers. LVP’s wear layer, ranging from 6 mil to 30 mil, provides superior protection against daily wear and tear, particularly in high-traffic areas. You’ll find that thicker wear layers greatly enhance the flooring’s durability and longevity.
Unlike traditional flooring that requires periodic refinishing and sealing for maintenance, LVP’s water-resistant protective layer maintains its appearance with minimal upkeep. The engineered wear layer shields against scratches, dents, and moisture damage, extending the flooring’s lifespan beyond 20 years when properly maintained. While standard vinyl flooring features thinner protective layers suitable only for low-traffic zones, LVP’s robust wear layer construction guarantees lasting performance across various applications, making it a more versatile and durable choice.
Impact and Scratch Resistance
Through rigorous comparative testing, LVP’s impact and scratch resistance markedly outperforms traditional flooring materials in key durability metrics. You’ll find that LVP’s enhanced wear layer provides superior protection in high-traffic areas, consistently outranking traditional flooring in scratch resistance assessments.
The rigid core construction of LVP delivers exceptional impact resistance, allowing it to withstand heavy furniture loads and daily wear without the denting commonly seen in traditional materials. Your LVP installation will maintain its structural integrity thanks to its water-resistant properties, eliminating concerns about warping or degradation in moisture-prone environments. The low maintenance requirements, coupled with a 20+ year durability rating, make LVP a technically superior choice for long-term flooring performance. These attributes guarantee sustained resilience under demanding conditions.
Long-Term Cost Benefits
Despite higher upfront costs, LVP’s extended 20+ year lifespan delivers substantial long-term cost advantages over traditional flooring alternatives. You’ll find significant savings through reduced maintenance requirements, as LVP only needs basic sweeping and occasional mopping, unlike traditional materials that demand specialized cleaning products and periodic refinishing. LVP’s enhanced durability in high-traffic areas translates to fewer replacements over time, while its superior water-resistant properties prevent costly moisture damage in kitchens and bathrooms. When you compare the lifetime investment, LVP’s robust wear layer protection against scratches and dents minimizes repair expenses that typically plague traditional flooring options. These features, combined with its 20+ year durability, result in measurable cost savings throughout the flooring’s lifespan, offsetting the initial investment through reduced maintenance and replacement costs. Additionally, LVP’s lower carbon footprint aligns with eco-conscious trends, making it an environmentally sustainable flooring choice.
Cost Analysis: Initial Investment and Long-Term Value
While homeowners often focus on initial costs, comparing luxury vinyl plank (LVP) with traditional flooring requires a thorough financial analysis. You’ll find LVP’s upfront cost of $2-$7 per square foot markedly lower than traditional hardwood flooring‘s $8-$15 range. This initial investment difference, combined with LVP’s 20-year lifespan and minimal maintenance requirements, creates substantial long-term value.
- Installation costs remain lower for LVP, requiring less specialized labor and fewer materials
- Water-resistant properties eliminate costly moisture damage repairs common with traditional options
- Maintenance expenses decrease markedly, avoiding hardwood’s 5-10 year refinishing cycles
- Premium aesthetics enhance property value without the high-end material costs
Your investment strategy should consider both immediate and future financial implications. LVP’s durability, combined with its ability to replicate high-end materials, provides a cost-effective solution that maintains its value throughout its lifecycle while delivering professional-grade performance in various environmental conditions.
Installation Methods and Requirements
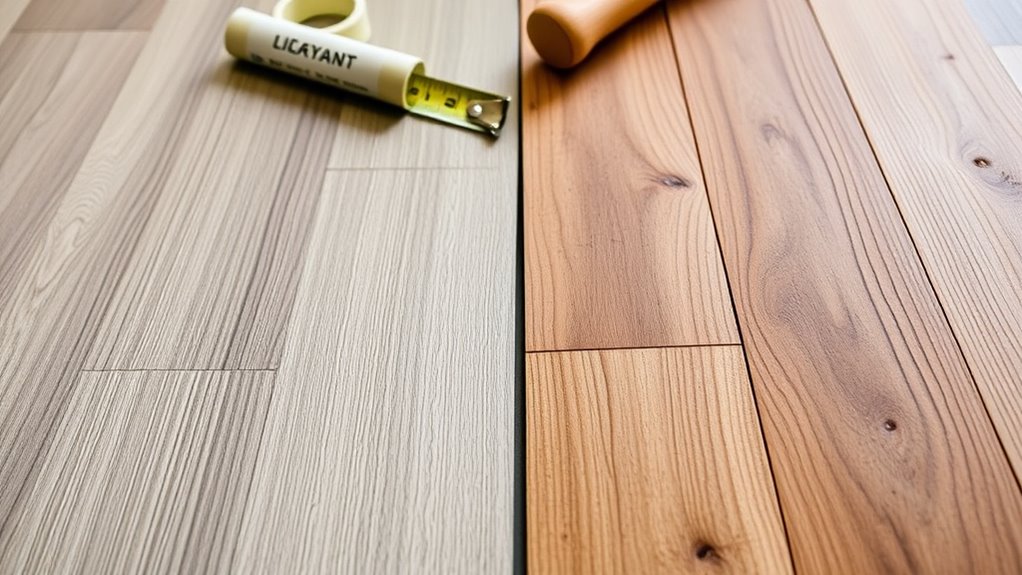
As modern flooring technology evolves, LVP’s installation methods have revolutionized the traditional flooring landscape. The click-lock installation system allows you to interlock planks without adhesives or fasteners, making LVP exceptionally DIY-friendly. You’ll find this method considerably reduces installation time compared to traditional adhesive installation required for some LVT products.
When evaluating your installation options, you’ll need to verify your existing flooring surfaces meet specific requirements. The subfloor must maintain ideal moisture levels, levelness, and cleanliness for maximum performance. While you can install LVP over most existing surfaces, professional installation might be advisable for complex layouts or permanent applications.
The installation timeline varies between methods. Click-lock LVP typically completes within a day, whereas adhesive installation necessitates additional drying time. You’ll need to factor this temporal consideration into your project planning, particularly if you’re managing multiple renovation phases simultaneously.
Maintenance and Care Considerations
When comparing maintenance requirements between flooring options, LVP and LVT systems demonstrate superior ease of care with minimal upkeep protocols. You’ll find these surfaces are remarkably resistant to stains and can withstand high-traffic areas without showing significant wear. Their water-resistant properties make them particularly suitable for moisture-prone environments, offering protection against water damage that often affects traditional flooring materials.
- Regular maintenance requires only basic sweeping and occasional damp mopping with pH-neutral cleaners
- 20+ year longevity achievable through proper care, eliminating need for refinishing
- Strategic placement of entrance mats captures 80% of incoming debris
- Avoid abrasive cleaning agents that can compromise the wear layer’s integrity
With minimal maintenance requirements and enhanced durability features, LVP flooring systems provide cost-effective solutions for both residential and commercial applications. The protective wear layer guarantees sustained performance while maintaining aesthetic appeal throughout the product’s lifecycle, making it an efficient choice for contemporary installations.
Environmental Impact and Sustainability
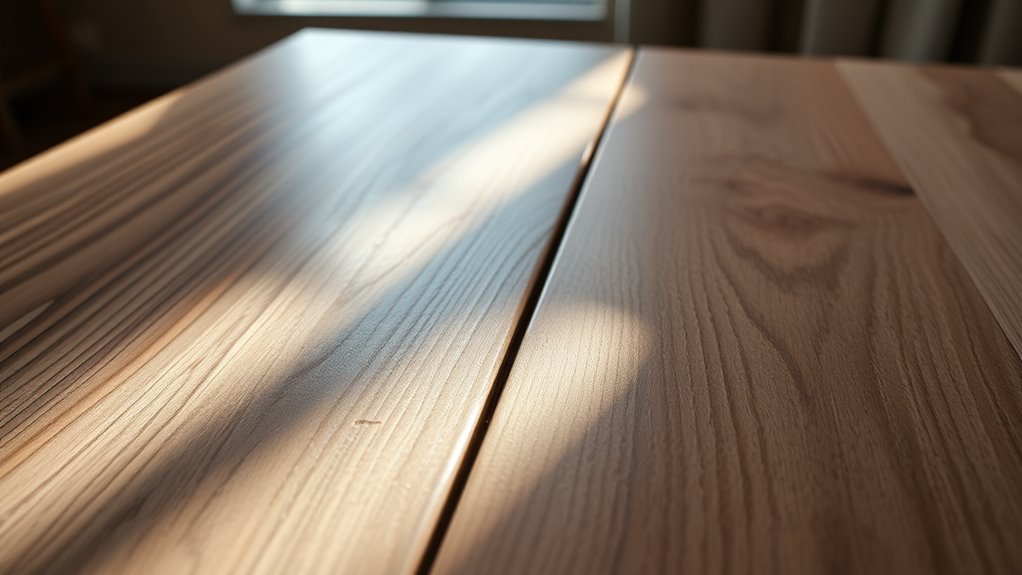
Despite their practical advantages, LVP and LVT flooring systems present significant environmental challenges due to their PVC-based composition and non-biodegradable nature. When you’re evaluating flooring options, you’ll need to take into account these materials’ substantial environmental footprint throughout their lifecycle, from manufacturing to eventual disposal.
While LVP and LVT’s synthetic materials offer enhanced water resistance and durability, their production processes emit volatile organic compounds that contribute to indoor air pollution. You’ll find that emerging recycling programs are addressing end-of-life waste disposal concerns, but these initiatives remain limited in scope. Some manufacturers now offer eco-friendly alternatives incorporating recycled content and sustainable manufacturing techniques, though these options still can’t match the environmental benefits of natural materials. As you weigh your flooring choices, keep in mind that while LVP and LVT may require less frequent replacement than traditional options, their long-term environmental impact raises concerns about sustainability and waste management in our ecosystems.
Making the Right Choice for Your Space
Selecting the ideal flooring solution requires careful analysis of your space’s specific requirements and usage patterns. When evaluating luxury vinyl planks against traditional hardwood, consider your room’s exposure to moisture, foot traffic intensity, and installation constraints. LVP’s water-resistant properties make it particularly suitable for areas prone to spills or humidity, while its enhanced durability withstands daily wear in high-traffic areas.
- Installation method: LVP’s click-lock system enables efficient DIY installation, reducing labor costs compared to traditional hardwood’s complex installation requirements
- Maintenance protocol: LVP requires minimal upkeep with basic cleaning, while hardwood demands periodic refinishing and specialized care
- Budget considerations: At $2-7 per square foot, LVP offers significant cost savings versus hardwood’s $5-15+ range
- Long-term performance: Both materials provide durability, but LVP’s superior resistance to water damage and scratches guarantees consistent appearance over time
Consider your lifestyle needs and budget constraints when making this significant investment in your home’s infrastructure.
Conclusion
While you’ve meticulously analyzed the 4.5mm thickness of LVP’s wear layer and scrutinized traditional hardwood’s 0.75-inch solid construction, isn’t it ironic that your final decision might come down to something as simple as aesthetics? Despite the technical specifications of wear ratings (AC3 vs. AC5) and extensive VOC emissions data, you’ll likely choose based on which flooring makes your space feel like home—though that 20-year warranty won’t hurt.